Je nach GFK-Hersteller erhalten Sie die faserverstärkten Kunststoffe als einzelne Platten oder als Rollenware – oder sogar beides. LAMILUX Composites hat beide Lieferformen im Repertoire und passt die Größen und Längen individuell an die Kundenbedürfnisse an. Das bedeutet aber: Sie als Kunde müssen Ihre Bedürfnisse kennen. Viel mehr noch: Sie müssen wissen, ob Platten oder Rollen Ihre Lager- und Produktionsbedürfnisse besser erfüllen und welche Maße für die Weiterverarbeitung in Ihrer Produktion ideal sind. Dann kann LAMILUX Ihnen Kunststoffplatten bis zu einer Breite von 3,20 Metern und einer Länge von bis zu 12 Metern fertigen. Auf eine Rolle wiederum passen bis zu 300 Meter GFK, je nach Dicke, die von 0,3 bis 3,0 Millimeter variiert. Platten können bis zu 5,0 Millimeter dick sein. Die Herstellungsweise ist bei all diesen Varianten die gleiche: Auf kontinuierlichen Flachbahnanlagen werden die faserverstärkten Kunststoffe mit stets gleichbleibend hoher und jederzeit reproduzierbarer Qualität gefertigt. Das bedeutet, dass Dicke, Farbe und Zusammensetzung innerhalb einer Platte oder Rolle sowie auch der nächsten Charge stets identisch sind.
Die Vor- und Nachteile von GFK als Rollenware
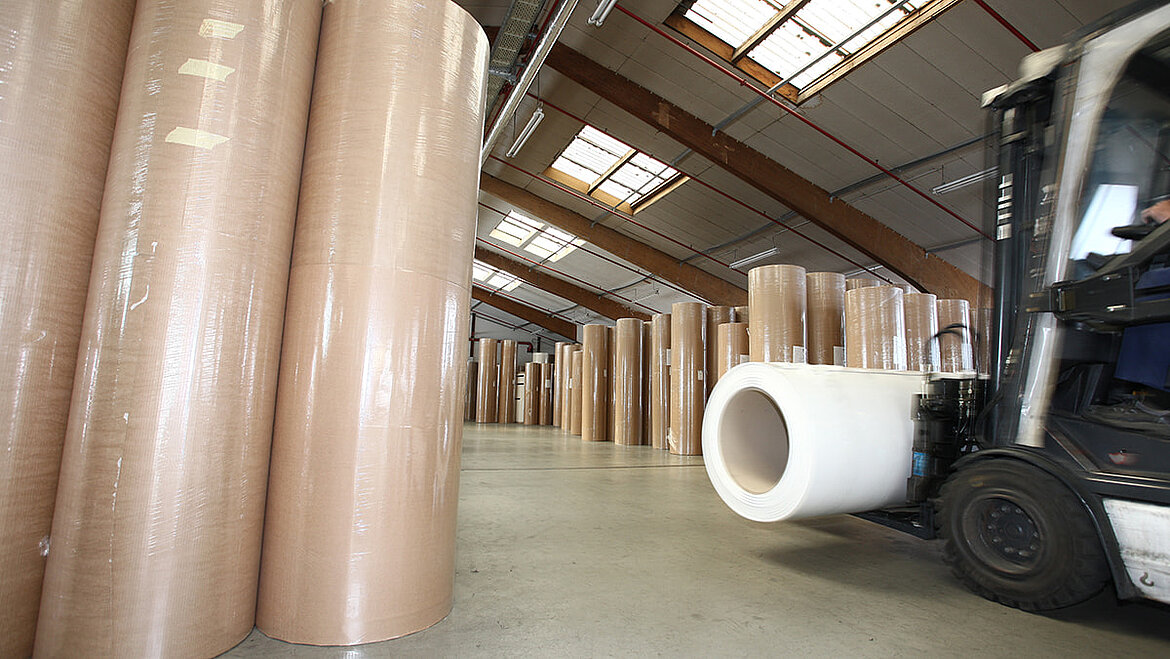
Fällt die Entscheidung auf GFK als Rollenware, macht sich das vor allem positiv in der Lagerkapazität bemerkbar: In der Regel werden die Rollen stehend gelagert, was deutlich weniger Platz einnimmt als die gleiche Menge GFK in liegenden Platten. Doch nicht nur bei der Lagerung, sondern auch schon beim Transport macht sich das als Vorteil bemerkbar: Auf einen Lkw passen wesentlich mehr GFK Rollen als Platten. Dadurch verringern sich neben der Lagerkosten eben auch die Transportkosten.
Auch in Ihrer Fertigung selbst können GFK Rollen Kosten reduzieren. Da deren Breite zwar festgelegt ist, aber die Länge des Zuschnitts frei wählbar ist, können individuell auf die Anwendung zugeschnittene Stücke abgetrennt werden.
Das erspart übergroße Reststücke und unnötigen Abfall. Preisersparnis gibt es bei GFK als Rollenware allerdings schon direkt beim Einkauf: Da beim GFK Hersteller der Zuschnitt wie bei GFK Platten wegfällt, kann sich der Meterpreis reduzieren.
Dieses Argument kann jedoch in der Weiterverarbeitung einiges an Kosten verursachen: Einerseits müssen Sie in Ihren Prozessen zusätzliche Arbeitsschritte integrieren, um die gewünschte GFK Länge vor Ort selbst zuzuschneiden. Dazu benötigen Sie zudem spezielle Werkzeuge und Ausstattung wie etwa eine Zuschnittanlage, Zuschnittwerkzeug, eine Abwickelvorrichtung sowie Equipment zum Rollenhandling wie etwa eine Rollenkluppe oder einen Stapler.
Ein weiterer Nachteil von GFK als Rollenware kann es werden, wenn an einer ungünstigen Stelle im Material ein rohstoffbedingter Fehler auftaucht – wie etwa ein Mattenfehler oder ein Gelcoatfehler. Dadurch kann mehr Abfall entstehen, wenn dieses Stück ausgespart werden muss.
Zuletzt ist ein wichtiges Kriterium für die Wahl von Platten oder Rollen als Lieferform von glasfaserverstärkten Kunststoffen, wie dick das Material für Ihre Anwendung sein soll. Zwar kann beispielsweise LAMILUX GFK in Dicken bis zu 5,0 Millimetern produzieren, doch aufrollen lassen sich nur Kunststoffbahnen aufgrund der hohen Eigensteifigkeit bis zu einer maximalen Dicke von 3,0 Millimetern. Allerdings gibt es auch Materialien mit noch höherer Eigensteifigkeit, sodass dieses sich nur bis zu einer Dicke von 2,0 Millimetern wickeln lässt.
Die Vor- und Nachteile von GFK als Plattenware
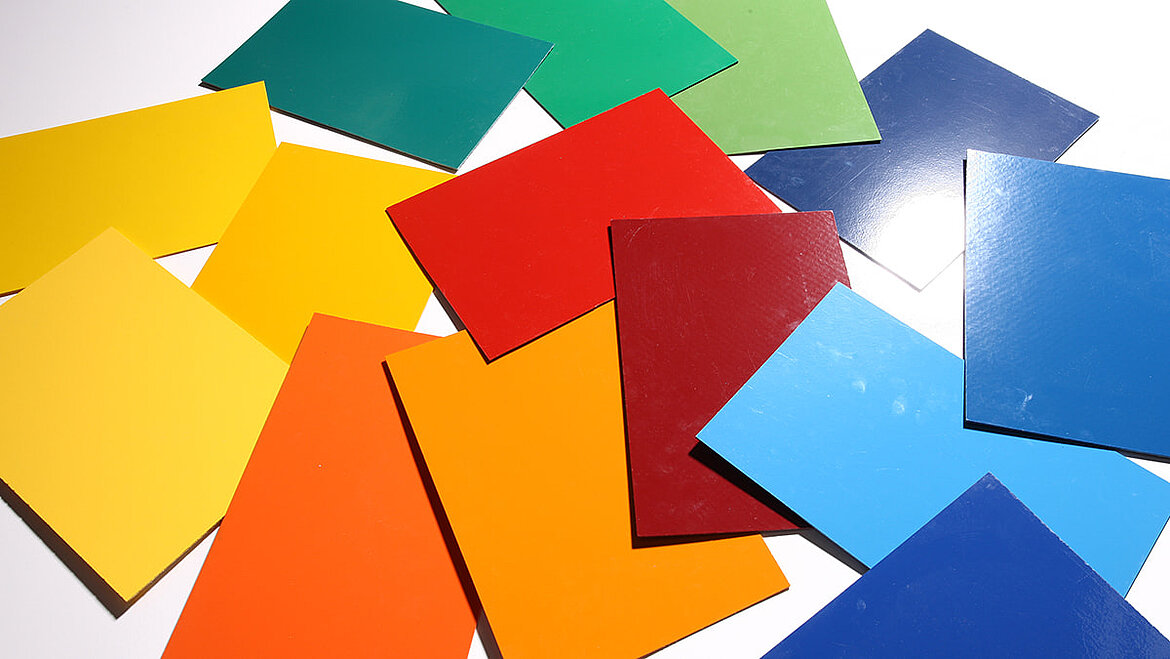
Aus den Vor- und Nachteilen von GFK als Rollenware ergeben sich gleichzeitig auch die Vor- und Nachteile von GFK als Plattenware. Doch hier noch einmal ausführlich:
Ganz klar ein Pro-Argument für GFK Platten ist die „Ready to Use“ Anfertigung. Als Weiterverarbeiter nennen Sie dem GFK Hersteller die exakten Maße, in denen Sie die Kunststoffplatten benötigen. Die für Ihre Anwendung maßgeschneiderten Platten können Sie dann direkt in Ihrer Fertigung einsetzen. Sie sparen sich somit einerseits Aufwand, Prozessschritte, aber auch die Zusatzinvestitionen für Werkzeug und Equipment für den Zuschnitt.
Ebenso auf Ihren Wunsch abgestimmt ist bei Kunststoffplatten auch die Dicke des GFKs. Anders als bei Rollenware gibt es hier keine Limitierung, die durch den Wickelprozess entsteht.
GFK, das dicker als 3,0 Millimeter ist, ist zu steif zum Rollen. Bei Plattenware ist dieses Kriterium uninteressant. LAMILUX fertigt deshalb GFK Platten in einer Dicke von bis zu 5,0 Millimetern. Dadurch entstehen besonders feste, steife und robuste Kunststoffplatten, die in Anwendungen mit extremen Anforderungen zum Einsatz kommen – beispielsweise bei Fassadenplatten oder Einhausungen.
Der größte Vorteil von GFK Platten mag jedoch ihre überschaubare Größe sein, weshalb mögliche Materialfehler direkt beim Hersteller LAMILUX identifiziert und die Platten aussortiert werden. Bei Rollenware von mehreren hundert Metern kann es hingegen schon einmal zu vereinzelten kleinen Materialfehlern kommen, die dann erst beim Weiterverarbeiten ausgesondert werden können.
Dennoch gibt es auch Nachteile der Liefer- und Lagerform Platte. Falls der Produktionsprozess kurzfristig andere Längen fordert, sind Sie mit GFK Platten dementsprechend unflexibel. Es bleiben Ihnen dann nur die Optionen zwei Teilstücke aneinanderzusetzen, falls das die Anwendung zulässt, oder eine neue Plattenbestellung mit angepassten Maßen aufzugeben. Hierbei ist dann noch die Frage: Geben das auch die Lagerkapazitäten her? Denn GFK braucht wesentlich mehr Lagerplatz, wenn es in Platten verwahrt wird, anstatt in Rollen. Jede zusätzliche Bestellung macht diesen Nachteil umso sichtbarer.
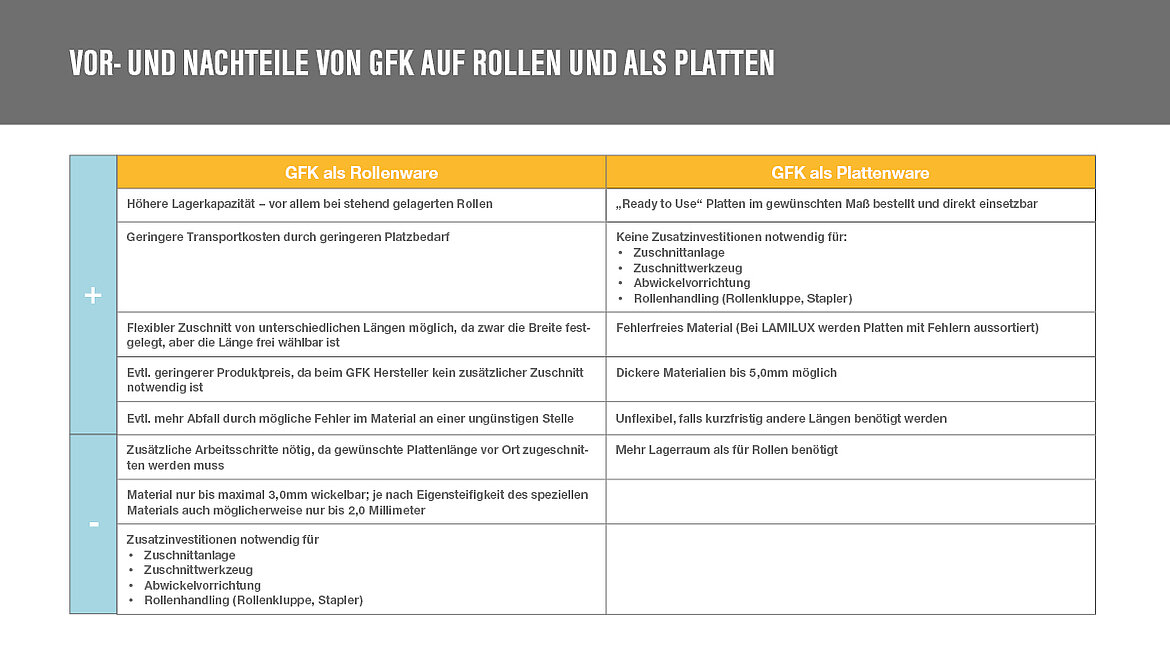
Welche Faktoren bei der GFK Auswahl noch wichtig sind
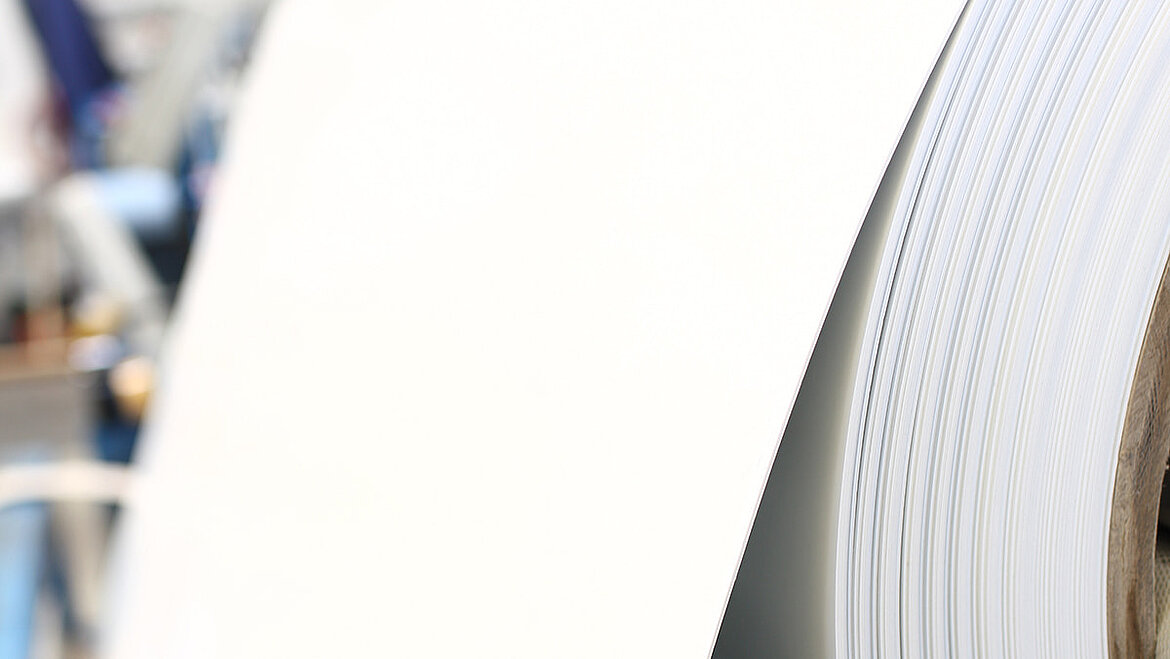
Um letztendlich das richtige GFK Produkt– also die passende Lieferform und die passende Materialzusammenstellung – für die eigene Produktion zu finden, sollten Sie die verschiedenen Hersteller in vier Kategorien vergleichen: Kosten, Service, Zuverlässigkeit und Qualität. Unter den Bereich Kosten fallen vor allem die oben in diesem Artikel bereits angesprochenen Kriterien: der Materialpreis an sich, Ausschuss und Abfall, Lager- und Transportkosten sowie die Kosten für den Rollen- bzw. Plattentausch in der Weiterverarbeitung. Im Bereich Service dreht sich alles rund um die Leistungen, die der GFK Hersteller über sein Produkt hinaus bietet. Kriterien hier sind zum Beispiel die Bedeutung von maßgeschneiderten Produktmustern, Lieferzeiten, Reaktionszeit bei Problemen und Fragen, Unterstützung in der Anwendungstechnik, Liefermengen, Innovationskraft, die Ausprägung und Größe des Produktportfolios.
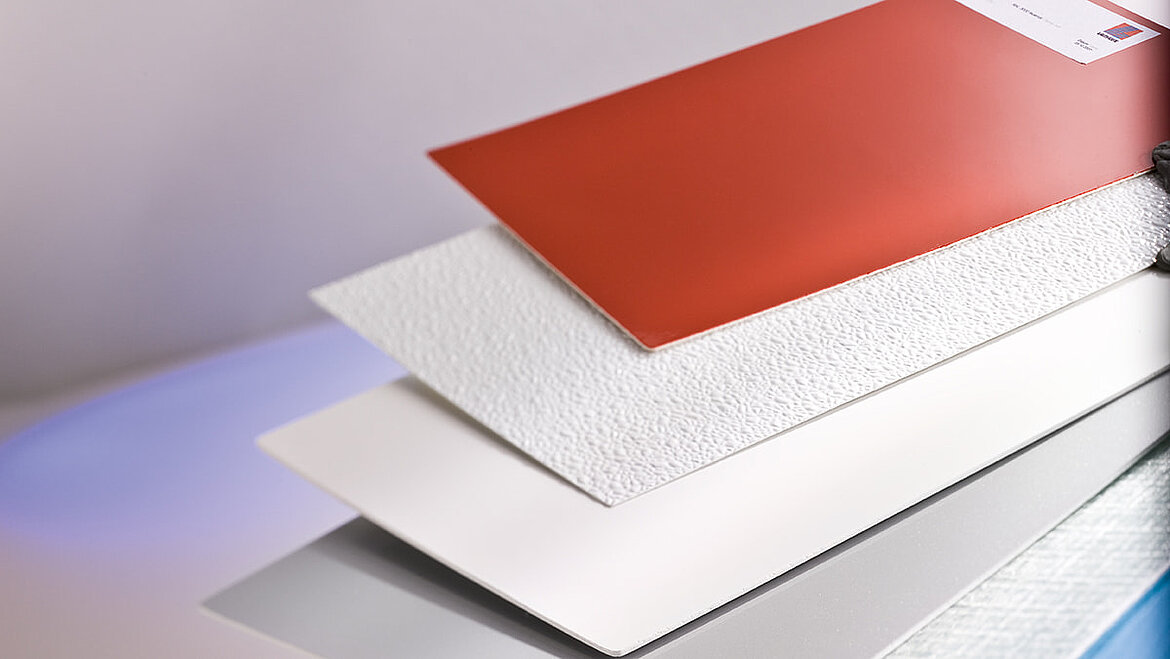
Auch LAMILUX bietet Produktmuster aller seiner GFK Materialien. Auf den jeweiligen Produktseiten können Sie diese kostenlos bestellen. Darüber hinaus müssen sie sich auch auf Ihren Zulieferer verlassen können: Werden die Versorgung mit ausreichenden Mengen und die vereinbarten Lieferzeiten eingehalten? Bleibt die Produktqualität konsistent hoch? Qualität ist auch das vierte Stichwort: Wie ist die generelle Produktqualität? Manche Hersteller lassen sich auch die Qualität ihrer Produktionsprozesse und Labortest von unabhängigen Prüfinstituten bescheinigen. Derlei Zertifikate geben viel Aufschluss über das letztendliche GFK Produkt. Ein Beispiel hierfür sind die TÜV-zertifizierten Prüfmethoden von LAMILUX. Als einziger GFK Hersteller weltweit hat LAMILUX 17 seiner teilweise selbstentwickelten Material- und Prozesstests vom TÜV Süd zertifizieren lassen und unterliegt damit strengen Qualitätsstandards.
GFK in Platten oder Rollen – Ein Fazit
Ein klarer Sieger lässt sich im Vergleich GFK Platten versus GFK Rollen nicht ermitteln – dazu sind die Wettkampfarenen zu divers. Beide Liefer- und Lagerformen haben ihre Berechtigung und empfehlen sich jeweils für unterschiedliche Anwendungsbereiche.