Werkstoffauswahl in Fertigung, Konstruktion und Lebenszyklus
Eine ordentliche Kalkulation und umfassende Planung berücksichtigen auch die Faktoren der Werkstoffauswahl. Eine Darstellung am Beispiel von Aluminium, Stahl und glasfaserverstärkten Kunststoffen (GFK) für Seitenwände, Dächer und Böden von Nutzfahrzeugen und Wohnmobilen soll Aufschluss über den Return on Investment im Fahrzeugbau geben.
Was ist Return on Investment?
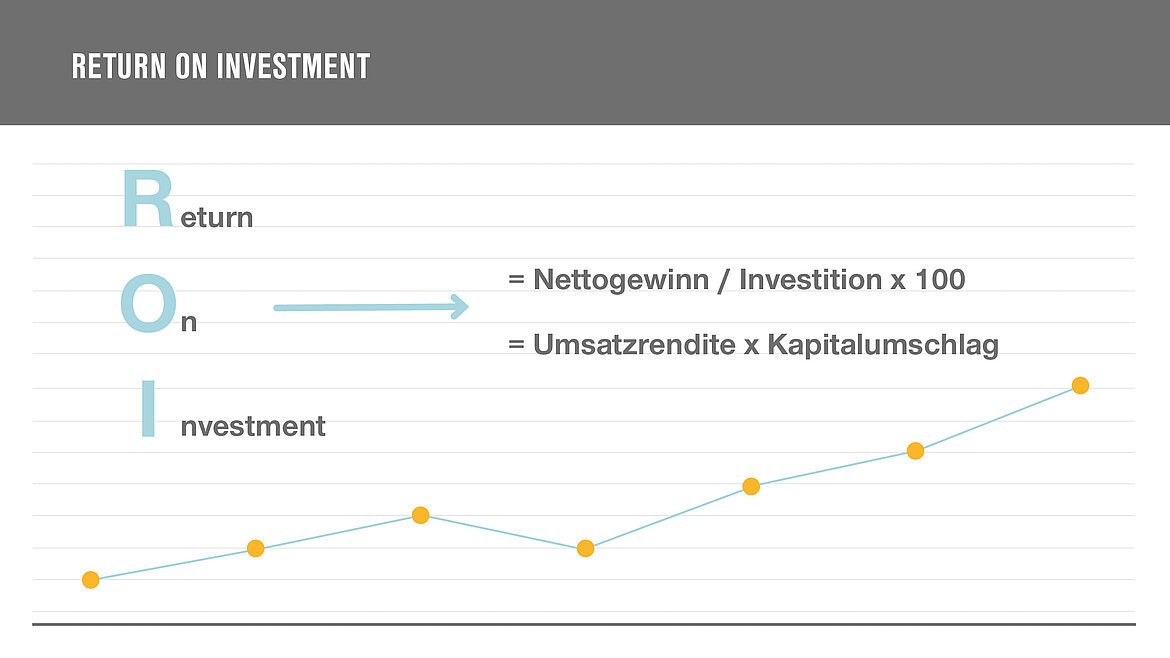
Der deutsche Begriff für Return on Investment (ROI) ist Kapitalrendite. Letztlich steckt dahinter das Konzept, dass man durch den Gewinn alle Investitionen wieder herein wirtschaftet.
Erst dann war eine Investition – wie etwa ein neuer LKW für die Flotte – erfolgreich.
Für die Berechnung des ROI gibt es zwei Möglichkeiten:
- (Gewinn / Investition) * 100
- Umsatzrendite * Kapitalumschlag
Daraus entsteht der ROI als prozentualer Wert, der bei einer lohnenden Investition bestenfalls über 10 ist. Erhöht sich die Umsatzrendite oder der Kapitalumschlag erhöht sich zwangsweise auch der Return on Investment. Dies geschieht entweder durch höhere Umsätze oder niedrigere Investitionskosten.
Wodurch erreichen Sie das – als Hersteller von Nutzfahrzeugen oder Wohnmobilen? Oder wodurch kann ein Transportunternehmen oder Wohnmobilverleiher seinen Return on Investment steigern? Möglichkeiten gibt es derlei viele. Eine ist die Auswahl der richtigen Werkstoffe für die Fahrzeuge.
Auswirkungen der Werkstoffauswahl in der Fertigung
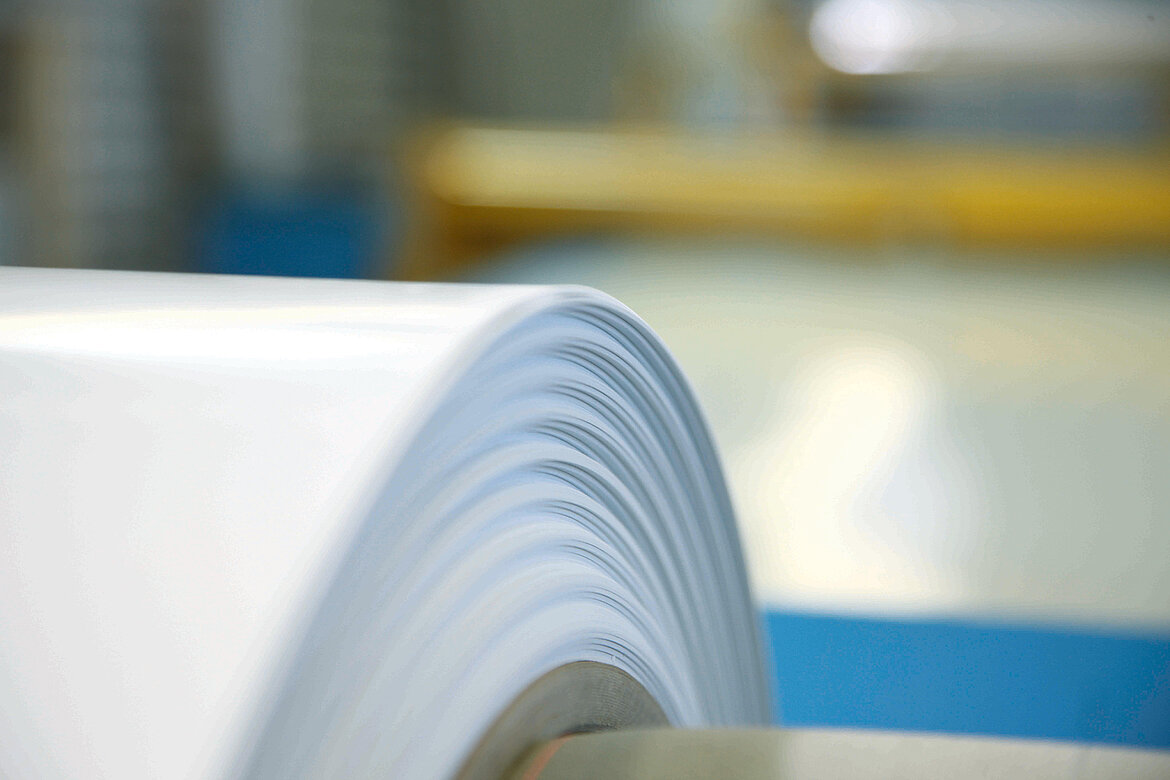
1. Die Lagerhaltung
Lagerplatz kostet Raum, Zeit und Geld. Deswegen ist bei jeder Werkstoffauswahl grundsätzlich auch zu überlegen, in welchen Formaten, Größen und Mengen ein Rohstoff eintrifft. Sowohl Aluminium als auch Stahl und GFK gibt es in großen Platten, exakten Zuschnitten oder als Rollenware. Je nach Organisation des Lagers wird eine dieser Varianten interessant. Am platzsparendsten ist die Rollenform. Da gerade die Konstruktionswerkstoffe für die Verkleidungen sehr dünn sind, enthält eine Rolle viele Laufmeter bei vergleichsweise geringem Durchmesser. Aufrecht nebeneinanderstehend nehmen die Materialrollen so weniger Raum in Anspruch als die gleiche Quadratmeterzahl an Plattenware. Zudem lässt sich GFK sogar bis zu einer Dicke von 3 mm problemlos auf handhabbare Rollen wickeln.
2. Die Verarbeitung
Sägen, Bohren, Nieten – Metallbleche zu verarbeiten ist kein Hexenwerk und durchaus auch ungelernten Arbeitern bekannt. Doch wissen Sie, wie man glasfaserverstärkte Kunststoffe weiterverarbeitet? Sie benötigen nur handelsübliche Werkzeuge. Ein weiterer Vorteil: Beim Schneiden oder Sägen von GFK entstehen keine derart scharfen Kanten wie bei Metallen, an denen der Verarbeiter sich schneiden und verletzen kann.
Zudem muss ein Werkstoff immer in seiner Kombination mit anderen Materialien betrachtet werden. Wie werden also Alu, Stahl oder GFK auf ihren Trägern befestigt? Die Metalle werden vorwiegend genietet. Das geht sehr schnell und bedarf nur wenig Übung. Langfristig betrachtet schafft man hier aber Schwachstellen für Korrosion und Wassereintritt in der Konstruktion. Verklebungen verhindern diese Problematik und sind mit einer kurzen Schulung ebenso leicht zu realisieren wie herkömmliche Arbeitsmethoden.
Zusätzlich ist es immer von Vorteil, Arbeitsschritte einzusparen. Dies ist mit Mehr-in-1-Produkten möglich. Dies sind Materialqualitäten, die bereits mehrere Funktionen in sich vereint tragen. Beispielsweise ein holzfreier Bodenaufbau, der aus gewebeverstärktem GFK mit integrierter PVC-Decklage besteht. Oder eine Innenwandverkleidung mit Velouroberfläche.
Beispielgebend für diese Produkte steht das 3-in-1-GFK LAMIfoamtex: Eine Schicht aus glasfaserverstärktem Kunststoff bildet den Träger. Darüber ist eine individuell anpassbare Schaumschicht als weicher Kern, der zwischen 2 mm und 8 mm hoch sein kann. Wie hart oder weich das Endmaterial sein soll und auch welche Schalldämmung benötigt wird, sind die ausschlaggebenden Kriterien für die Wahl der Schaumstoffdicke und des Raumgewichtes. Darauf folgt die oberste und auch für den Nutzer sichtbare Schicht, eine kundenspezifische Dekorlage, wie beispielsweise Kunstleder, Gewebe, Velours oder Vlies.
Dem Caravan- oder Bushersteller bieten sich aber noch mehr Vorzüge. Mittels einer innovativen Methode werden die drei Schichten ohne Klebstoff verbunden. LAMIfoamtex ist somit wesentlich leichter, umweltfreundlicher und nachhaltiger als die herkömmlichen Lösungen, die vom Kunden selbst aufwendig mit Stoffen beklebt werden müssen. LAMIfoamtex hat ein Flächengewicht von 1,65 kg/m², wohingegen ein Sperrholzdekor bei einer Stärke von 4 mm zirka ca. 2,4 kg/m² wiegt. Schon bei einer Innenwandfläche von 18 Quadratmetern würde der Holzverbund 13 Kilogramm mehr wiegen als LAMIfoamtex. Das sind 30 % des Flächengewichts. Eine verkürzte Prozesskette steht also nur am Anfang, es folgen Arbeits-, Zeit-, Gewicht- und Materialeinsparungen.
3. Der Produktionsausschuss
Um den Produktionsausschuss zu betrachten, müssen wir noch einmal zur Lagerhaltung zurückkehren. Denn bereits hier unterscheiden sich die Materialien deutlich voneinander: Sowohl die Platten als auch die Rollen aus Aluminium und Stahl sind anfällig für Transport- und Lagerschäden. Diese beiden Werkstoffe lassen sich derart leicht verbiegen und verbeulen, dass schon ein Schwenk mit dem Gabelstapler oder ein heruntergefallener Hammer das Blech eindellen können. Dann bedarf es großer Anstrengung, das Aluminium oder den Stahl wieder zu glätten. Nicht immer ist das möglich. Bei GFK verhält es sich anders: Der Kunststoff ist schlag- und stoßfest, sodass auch eine punktuelle Krafteinwirkung den Werkstoff nicht dauerhaft verformt.
Bei Aluminium oder Stahl entstehen bei Stößen oder Schlägen im ungünstigsten Fall sogar Löcher. Diese sind dann nicht mehr unsichtbar und bei gleichbleibender Funktionalität zu reparieren. Es fällt demnach je nach Stelle und Größe der Beschädigung mehr oder weniger Material als Ausschuss an. Passiert es bei GFK, dass es durch unvorsichtige oder unsachgemäße Handhabung beschädigt wird, kann die Stelle partiell durch Spachteln, Schleifen und Lackieren repariert werden. Auch den Gelcoat mit seinen schützenden Eigenschaften kann man bei einer Ausbesserung wieder auflaminieren.
Ein weiterer Faktor für hohen Produktionsausschuss sind Randstücke, Zuschnitte oder Aussparungen, die Sie nach dem eigentlichen Arbeitsschritt nicht mehr verwendet werden können. Um hier Material, Arbeitsschritte und Entsorgungskosten zu sparen, muss der Werkstoff so passgenau wie möglich sein. Individuelle Maßanfertigungen in Längen und Breiten machen dies möglich. Der GFK-Hersteller LAMILUX liefert seine faserverstärkten Kunststoffe maßgeschneidert bis zu einer Breite von 3,20 Metern und in beliebiger Länge. Das erspart einerseits unnötigen Ausschuss und andererseits macht es zahlreiche Zuschnitte unnötig. So vermeiden Sie zudem auch Stöße der Platten auf der fertigen Fläche, da Sie bereits passgenaues Material verwenden.
Auswirkungen der Werkstoffauswahl auf die Konstruktion
Der aktuell wohl größte Trend im Fahrzeugbau ist der Leichtbau. Unabhängig ob Benzinmotor oder E-Mobilität: je leichter ein Fahrzeug, desto besser für Umwelt, Image und die laufenden Kosten. Gewicht einzusparen, verringert dem LKW-Flottenbetreiber die Energiekosten und erlaubt dem Caravanbesitzer eine höhere Zuladung. Bei diesem Punkt gewinnen Aluminium und GFK gegen Stahl, sie sind die deutlich leichteren Werkstoffe. Wird die Robustheit noch ein Kriterium, so hat GFK insgesamt die Nase vorn.
Doch trotz aller Robustheit, kann auch bei GFK-Verkleidungen einmal ein Schaden entstehen. Beschädigungen wie Löcher oder Risse lassen sich aber unkompliziert und ohne das Material auszutauschen reparieren. Die Stelle wird ausgespachtelt, geschliffen und anschließend neuer Gelcoat auflaminiert oder die Stelle lackiert – quasi eine OP am offenen Herzen, aber ohne Narben. Bei Aluminium und Stahl ist dies nicht möglich. Die Stelle wird hier entweder sichtbar überklebt oder das komplette Verkleidungsteil wird ausgetauscht.
Auswirkungen der Werkstoffauswahl auf den Lebenszyklus
Im Leben eines Wohnmobils oder eines LKWs passiert so einiges – vor allem vieles, was man nicht voraussehen kann. Dennoch wappnet der passende Werkstoff das Fahrzeug vor äußeren Einflüssen wie beispielsweise Sonne, Wasser oder mechanischer Belastung. Denn einerseits leidet darunter die Optik, andererseits aber auch die komplette Konstruktion.
1. Wasser und Feuchtigkeit
Aluminium und Stahl sind anfällig für Korrosion und Rost. Eine typische Eigenschaft von Metallen. Wir kennen alle die LKW, deren Auflieger Rostblumen ansetzen. Bei GFK ist das anders: Die Glasfasern und das verwendete Harz sind korrosionsfrei. Auch das Streusalz im Winter, worunter Metall enorm leidet, hinterlässt bei GFK keine Spuren.
2. Hagel, Stöße und Schläge
Wie auch schon bei der Verarbeitung von Metallen verhält es sich im Lebenszyklus des Fahrzeugs: Aluminium und Stahl bleiben verformbar. So richten sowohl Hagel an den Außenflächen oder auch Stöße durch das Be- und Entladen kleine bis große Schäden an: Die Oberflächen bekommen Dellen, Beulen oder gar Löcher, die aufwendig repariert werden müssen, falls überhaupt möglich. Auch hier setzt sich GFK bei der Werkstoffauswahl durch: Das Material ist schlagzäh, robust und durch Hagel oder Stöße nicht deformierbar.
3. Sonneneinstrahlung und Hitze
Bleichen die Außenflächen nach einigen Jahren oder schon Monaten aus oder bekommen sie gar Hitzeblasen und Wärmeverformungen, ist guter Rat oft teuer. Hier scheiden sich gute Materialien von sehr guten – sogar innerhalb des Werkstoffs GFK selbst. Vergleichen Sie auf den folgenden beiden Bildern einmal die Seitenwände von Wohnmobilen aus unterschiedlichem GFK nach einem beziehungsweise nach drei Jahren.
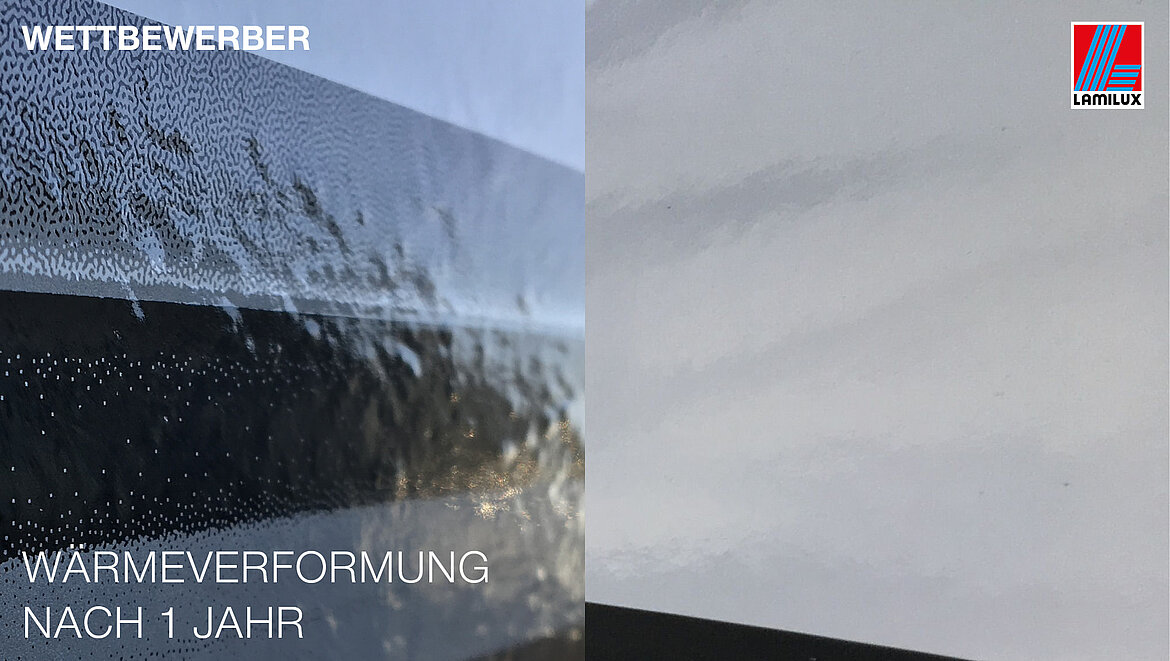
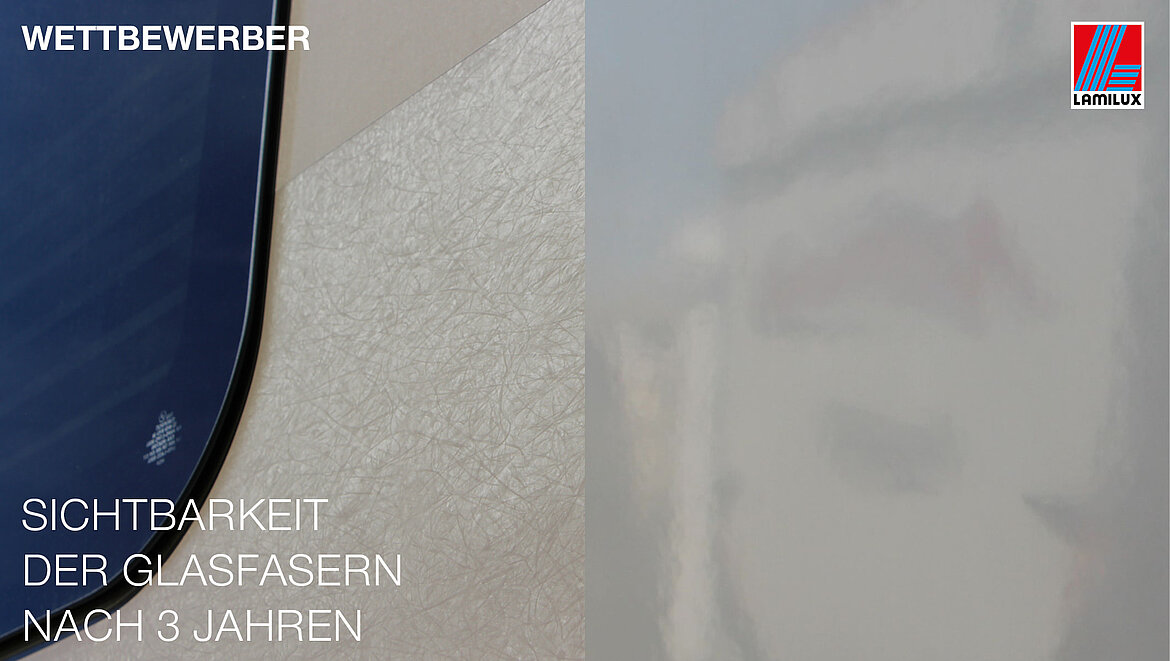
Sie sehen: GFK ist auch nicht gleich GFK. Sowohl die verwendeten Rohstoffe als auch die Qualität und die Produktionstechnologie machen bei faserverstärkten Kunststoffen einen großen Unterschied in Performance, Langlebigkeit und Optik. Das zeigt, dass auch innerhalb einer Werkstofffamilie die Auswahl noch groß ist und sich dabei maßgeblich auf den Lebenszyklus eines Fahrzeugs auswirkt.